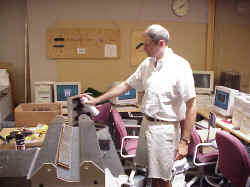 |
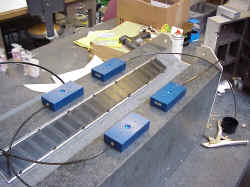 |
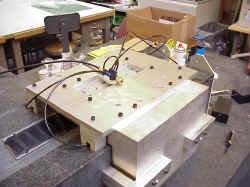 |
Step 1: Drew cleaning the Axtrusion way |
Step 2: the rough placement of the top bearings on the
way |
Step 3: The carriage is lower in place and the top
bearings positioned correctly. Then a vacuum is drawn through the top bearings to hold
them in place. |
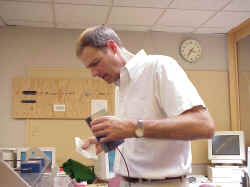 |
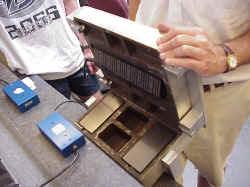 |
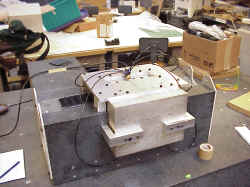 |
Step 4: Drew degreasing the surfaces of the bearing that
the epoxy will bond to. |
Step 5: Place side bearings in carriage |
Step 6: The carriage (w/ side bearings in place) is
lowered back on to the top bearings and the way. Fine adjustments are made in position of
the side bearings within the carriage. Then a vacuum is drawn through the side bearings to
secure them to the way. |
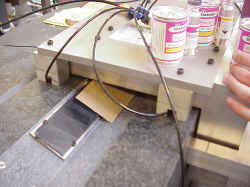 |
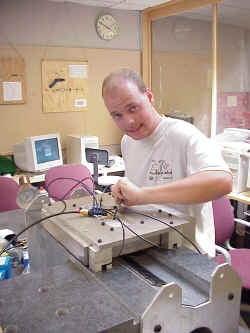 |
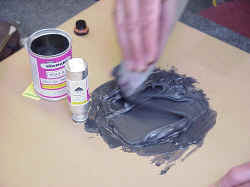 |
Step 7: A piece of cardboard that is the correct
thickness to set the air gap between the motor coil and magnet track is placed between the
two. |
Step 8: Our hero (me) lowers the motor coil down onto the
cardboard space to set the correct air gap and place the carriage under the its actual
loading condition |
Step 9: Now a batch of epoxy is mixed up to hold the
bearings in place |
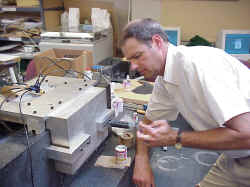 |
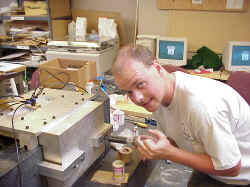 |
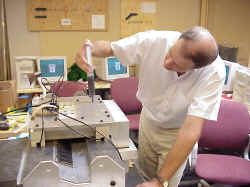 |
Step 10: Drew injects the epoxy into the side bearing
pockets. |
Roger continues to inject epoxy into the side pockets. |
Drew inject epoxy into one of the top bearing pockets. |
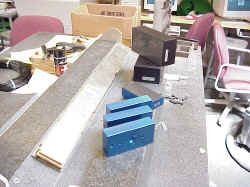 |
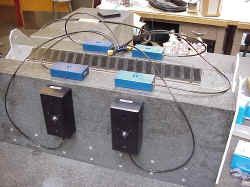 |
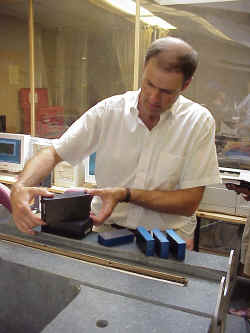 |
The six (6) Newway Bearings used in the Axtrusion
carriage. Four (4) 50 x 100mm and two (2) 75 x 150 mm. |
Look Mom!!! No Hands!!! The bearings can be
locked in place on the way by drawing a vacuum through them. This ensures that they
are accurately aligned with the way. |
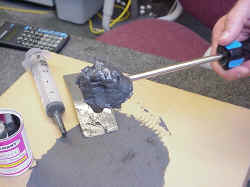 |
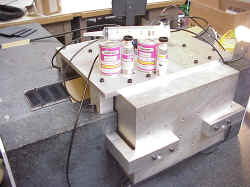 |
The semi-fluid viscosity epoxy was used so that it would not make a
huge mess when injected into the bearings and motor pockets. |
Look at that cool epoxy on the carriage (subliminal message, buy
Moglice buy Moglice... you are getting sleepy etc. etc.) |
Drew posing with his way cool bearings |